KMA ULTRAVENT® air extraction and filtration systems
Extraction devices and additional options
Tailor-made fume extraction devices
The fume collection near the source of emission is crucial for the air quality in the production hall. However, it is essential that this does not hinder the production process. Therefore, the proven KMA ULTRAVENT® module system offers for each die casting machine the correct fitting extraction device to meet all production requirements anytime.
Extraction hoods
For heavy-duty machines ULTRAVENT® extraction hoods are available in one and two-piece versions. If required, the regular or space-saving telescopic hoods can be moved aside, sliding on rails. The movement is carried out either manually or by a hood motor drive. Thus, an entirely free crane access for die change or servicing of the die machine is ensured anytime.
Due to the special hood design inside the hood (deflector plates) even strong and intermittent fume emissions can be securely collected and removed. Flow baffle plates ensure that the main air suction effect is focussing on the emission-critical areas of the hood’s bottom edges.
Open for free access
Fume extraction hood, open for free access
Fume extraction hood, closed and in operation
Air curtain system
Air curtain systems are used where limited space or other obstructions at the workstation will hinder the installation of extraction hoods. The KMA air curtain system consists of two elements: the blower unit that is attached to one end of the machine, generating an entirely adjustable horizontal air current above the source of emission. The second element is the extraction unit placed at the opposite end, receiving the air current including the contaminated air stream from the machine.
Air curtain systems usually require a higher extraction capacity than a comparable hood, because they do not have the possibility of buffering thermally rising fumes. However air curtains offer the advantage that the working area is not covered or obstructed by a suction device.
Large potential savings due to frequency converters (FC)
Air movement in production processes is a major consumer of energy. Blowers without a frequency converter (FC) run constantly at 100% capacity. Dampers control the air flow and thereby consume energy. The ECO+ technology offered by KMA represents an alternative with maximum energy efficiency. ULTRAVENT® ECO+ systems are equipped with a frequency converter for fan speed control. Thus, the speed can be adjusted according to requirements. Even a small reduction in speed leads to significant energy savings. In case of connection to the control of the manufacturing machine, a permanent speed adjustment is possible. The result often is an additional energy cost savings potential of up to 50 %.
Heat recovery
Provided that the purified air is to be conducted outdoors, the ULTRAVENT® filtration system can be upgraded by heat exchanger cells.
Fin tube heat exchanger
The warm exhaust air from the machines is lead to a central ULTRAVENT® filter system with integrated fin tube heat exchanger. Finned heat exchangers consist of a plurality of fins, which are bound to the core tubes by pressed on. Fin tube heat exchangers work on the gas-/ liquid-principle. Here, the heat-conducting fluid flows - in the form of brine or cold agent through the core tubes, while the gas or the hot exhaust airflows between the fins. The heated fluid is supplied for heating the supply air. Finned heat exchangers are efficient and can achieve good efficiencies due to the good heat transfer and large surfaces. The constantly high efficiency of the heat exchanger is secured by the use of the automatic ULTRAVENT® cleaning system.
Optionally with high-efficiency heat pump
At low temperature-process the efficiency can be increased by the integration of an Ambitherm® heat pump and the process heat can be generated from 30 °C to 60 °C (e.g. for heating up inlet air or domestic hot water) The Ambitherm® system ensures a direct transfer of the energy to the follow up process without a buffer tank. The coefficient of performance (COP > 6) is significantly higher than many comparable systems. The result: an extremely economical operation. Exhaust a
Exhaust air filtration in WINTER : economic heating of the hall with waste heat

Exhaust air filtration with heat recovery and heat pump:
- Fumes from die casting machines;
- central filter with precipitatot and heat exchanger;
- The purified and cooled exhaust air flows outdoors;
- The heat pump generates hot water ( 40 °C) for heating;
- Makeup air passes through an air heat exchanger - where it is heated up - into the hall
* Example data
Exhaust air filtration in SUMMER: cooling of makeup air with exhaust air
Exhaust air filtration with makeup air cooling and heat pump:
- Fumes from die sting machines;
- central filter with precipitator and heat exchanger;
- The purified and heated exhaust air flows outdoors;
- The heat pump generates cool water ( 12 °C) for cooling;
- Makeup air passes through an air heat exchanger - where it is cooled down - into the hall
* Example data
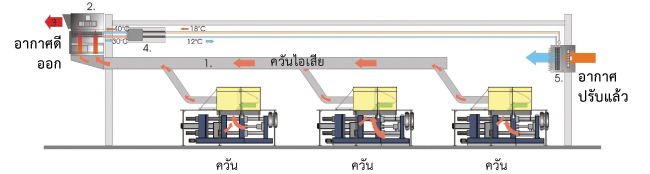